In the past, traditional construction projects mainly used red bricks (clay bricks) as wall materials. However, with increasing environmental awareness and stricter regulations, the use of solid clay bricks is now heavily restricted in urban construction. In particular, the use of solid bricks with a strength grade below MU10 is strictly prohibited in buildings with more than five floors. In many advanced regions, such as the Jiaodong area of Shandong Province, red brick production has been completely banned. The local government has enforced the use of environmentally-friendly lightweight bricks, and design units are required to specify their usage during the building design process. If red bricks are used, quality inspection departments will not approve the project.
This shift has created a significant demand for lightweight bricks, leading to a shortage in the market and attracting investors looking to enter the industry. Despite the high costs of importing advanced lightweight brick equipment, many manufacturers have faced challenges in the production process, which often lead to various types of damage and affect overall profitability.
Henan Huayi Machinery Manufacturing Co., Ltd., a modern high-tech enterprise specializing in the production of lightweight brick equipment, understands these challenges. Our goal is not just to sell machines but to ensure our customers succeed. With years of experience and technical expertise, we provide practical solutions to prevent common issues during the production of lightweight bricks.
Here are some of the most common problems encountered during the autoclaving process and how to avoid them:
1. **Black Heart**
This occurs when the center of the product appears darker or dull. It's usually caused by insufficient steaming. Check if the steam meets the requirements, whether the autoclave curing system is functioning properly, and ensure all equipment is in good condition. Also, review the raw materials and make necessary adjustments.
2. **Cracks**
Cracks can occur due to improper raw material mixing, incorrect green body strength, or an unbalanced autoclave curing system. Factors like water-to-material ratio, pouring temperature, mix ratio, and parking environment also play a major role. Ensuring proper preparation and careful operation can help reduce cracking.
3. **Adhesion**
Adhesion happens when blocks stick together after autoclaving. This is often due to moisture in the gaps between blocks and improper blocking techniques. Adjusting the moisture content, cutting joint width, and ingredient ratios can help prevent this issue.
4. **Bursting**
Bursting occurs when the surface of the product peels off, creating pockmarks. This is usually caused by burnt lime particles or agglomerates that expand under high heat. Proper mixing and ensuring adequate digestion of lime before autoclaving can prevent this problem.
5. **Surface Pits and Collapse**
These issues are often caused by condensed water in the pipeline. Modern autoclaves now have side air intakes, but it’s still important to avoid direct exposure of the blanks to water. Proper maintenance and setup can help avoid these damages.
6. **Mucosa (Sticking)**
Mucosa is a common issue during the pouring and cutting stages. It typically results from improper oiling of the bottom plate, low oil viscosity, or residual adhesives on the mold. Ensuring proper oil application and regular cleaning of molds can significantly reduce sticking.
At Henan Huayi, we are committed to providing not only high-quality equipment but also comprehensive support to ensure our clients achieve long-term success. Your satisfaction is our greatest reward, and we strive to deliver excellence in every aspect of our service.
If you're looking to invest in the aerated concrete industry, our recommended equipment includes aerated concrete machines and aerated concrete block production systems.
Contact us today to learn more about how we can help you build a successful and sustainable business in the brick manufacturing industry.
Chromium Oxide Abrasive
The high chromium wear-resistant alloy steel balls produced by our company have the following advantages:
1. With extremely high hardness, usually between 60-66 HRC, it can effectively resist wear and grinding and extend service life.
2. Excellent wear resistance, able to maintain stable performance during high-speed grinding and grinding, reducing the risk of wear and fracture.
3. It has good impact resistance and can withstand greater impact force and is not easy to break during high-speed grinding and grinding.
4. It has good corrosion resistance, can maintain stable performance in wet and corrosive environment, and is not easy to rust and corrosion.
5. Can maintain stable performance in high temperature environment, not easy to deform and soften, suitable for high temperature grinding and grinding process.
6. The wear rate of the steel ball is low, which can reduce the loss of abrasives and materials and improve the grinding and grinding efficiency.
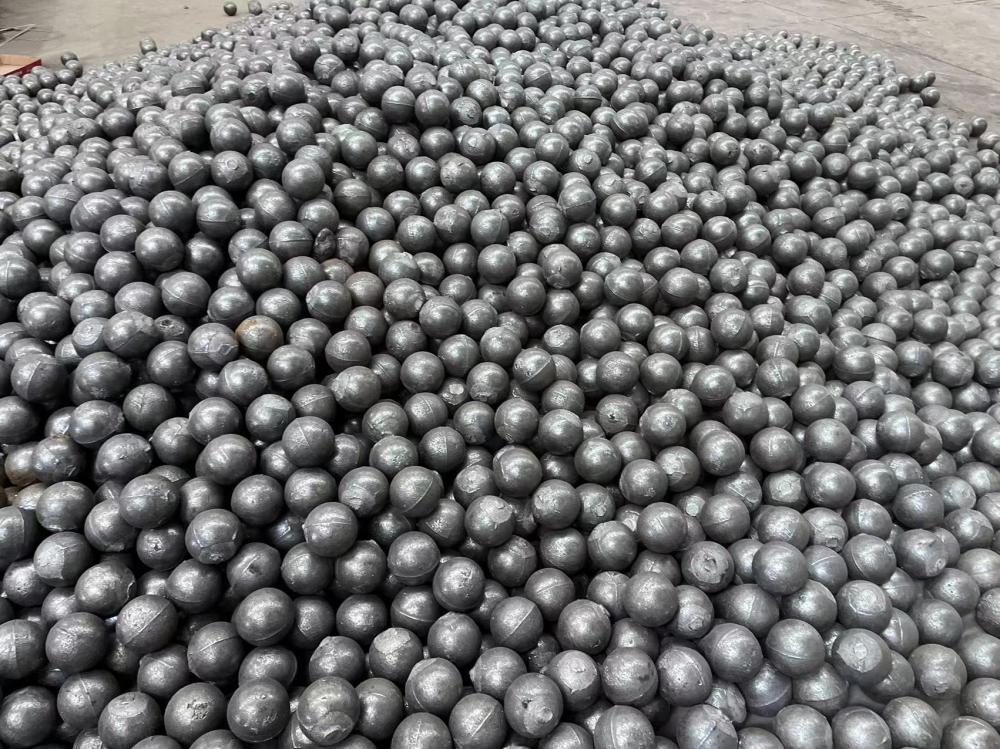
Chromium Oxide Abrasive,Alloy Steel Ball,Tempered Alloy Steel Balls,Wear Parts Steel Ball
Xuzhou Surun wear-resistant material Co., LTD , https://www.suruntools.com