As we all know, traditional wall materials in the construction industry were primarily made of red bricks (clay bricks). However, with environmental and structural concerns growing, many governments have imposed strict restrictions on the use of solid clay bricks. In urban areas, it's now illegal to use solid bricks with a strength grade lower than MU10 in buildings with more than five floors. In some advanced regions, red bricks have been completely banned. For example, in the Jiaodong region of Shandong Province, local authorities have strictly prohibited the red brick market and mandated the use of environmentally friendly lightweight bricks. Design companies are now required to specify the use of these eco-friendly materials in their blueprints, and any use of red bricks will result in rejection by quality inspection departments. As a result, the demand for lightweight bricks has surged, creating new opportunities for entrepreneurs and investors in the production sector.
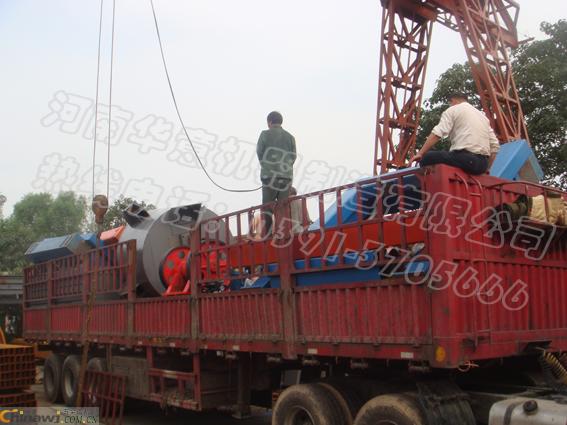
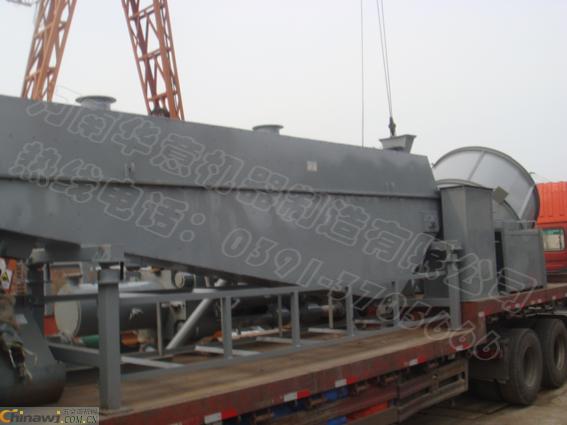
Setting up a lightweight brick production line often requires significant investment in advanced equipment. However, many manufacturers face challenges during the production process, such as damage and inefficiencies that negatively impact profitability. This has become a major concern for many in the industry. Henan Huayi Machinery Manufacturing Co., Ltd., a modern high-tech enterprise specializing in lightweight brick equipment, has focused on customer satisfaction and long-term success. With years of experience and technical expertise, our team of professionals is here to share practical solutions to prevent common issues in the production of lightweight bricks.
There are several key stages where problems can occur, especially before and after autoclaving. Here are some common issues and how they can be addressed: 1. **Heart or Black Core** Sometimes, the center of the brick appears darker or duller, known as a "heart" or "black core." This usually happens due to insufficient steaming. To fix this, check if the steam supply meets the requirements, ensure the autoclave curing system is functioning properly, and verify that the raw materials are correctly prepared. 2. **Cracks** Cracking is a common issue in lightweight brick production. It can be caused by improper raw materials, incorrect curing conditions, or even poor green body strength. Adjusting the water-to-material ratio, pouring temperature, and mix proportions can help reduce cracking. 3. **Adhesion** Adhesion occurs when blocks stick together after autoclaving. This is often due to moisture, gap width, or material composition. Ensuring proper blocking and cutting techniques, along with correct curing settings, can minimize adhesion. 4. **Bursting** Bursting refers to surface pockmarks caused by over-burned lime particles or other unprocessed materials. These particles may expand rapidly under high temperatures, damaging the product. Controlling the mixing process and ensuring proper curing conditions can help prevent this issue. 5. **Surface Pits and Collapse** These issues are often linked to condensation in the pipeline. Improper placement of intake pipes can lead to water damage. Modern autoclaves now feature side air intakes, but care should still be taken to avoid direct exposure of the blanks to condensation. 6. **Mucosa (Sticking Mold)** Mucosa occurs when the mold doesn't release properly, often due to inadequate oiling or poor maintenance. Using the right type of oil, ensuring the bottom plates are clean, and maintaining proper temperature control can help prevent sticking molds. At Henan Huayi, we are committed not only to delivering high-quality equipment but also to supporting our customers' long-term success. Your satisfaction is our goal, and our promise is to provide excellent products and reliable after-sales service. We welcome both domestic and international clients to visit and learn more about our solutions. Whether you're looking to invest in aerated concrete equipment or lightweight brick production systems, we’re here to help you succeed. Let us support your journey in the brick industry with professional guidance and innovative technology. Phone: [Insert Phone Number]
The high chromium wear-resistant alloy steel balls produced by our company have the following advantages:
1. With extremely high hardness, usually between 60-66 HRC, it can effectively resist wear and grinding and extend service life.
2. Excellent wear resistance, able to maintain stable performance during high-speed grinding and grinding, reducing the risk of wear and fracture.
3. It has good impact resistance and can withstand greater impact force and is not easy to break during high-speed grinding and grinding.
4. It has good corrosion resistance, can maintain stable performance in wet and corrosive environment, and is not easy to rust and corrosion.
5. Can maintain stable performance in high temperature environment, not easy to deform and soften, suitable for high temperature grinding and grinding process.
6. The wear rate of the steel ball is low, which can reduce the loss of abrasives and materials and improve the grinding and grinding efficiency.
Chromium Oxide Abrasive,Alloy Steel Ball,Tempered Alloy Steel Balls,Wear Parts Steel Ball
Xuzhou Surun wear-resistant material Co., LTD , https://www.suruntools.com